Aluminized Steel
Aluminised steel coil is obtained by aluminizing, which is a modern-day engineering innovation allowing the manufacture of high-heat resistance aluminised steel sheets at low costs with niche applications.
Aluminizing, above all, is a thermo-chemical diffusion process & is particularly applied to base metals like carbon steel, alloy steel, stainless steel, nickel-based alloys & nickel-iron alloys.
The physical properties of the aluminized product so obtained depend on the base metal used as well as the coating process & coating agents namely aluminum or its alloys. Demonstrably, the aluminized products, all the more, show good resistance to oxidation as well as excellent corrosion resistance by contrast to Galvanized steel products.
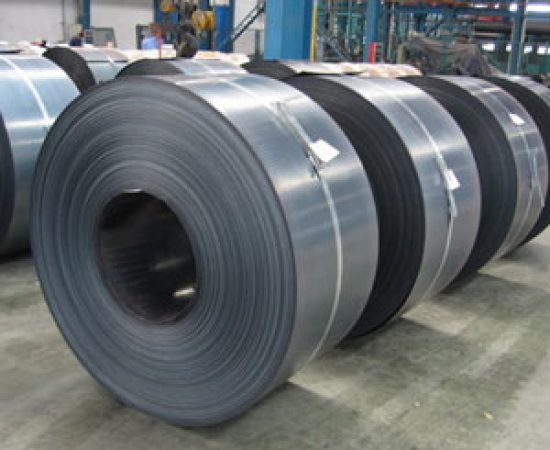
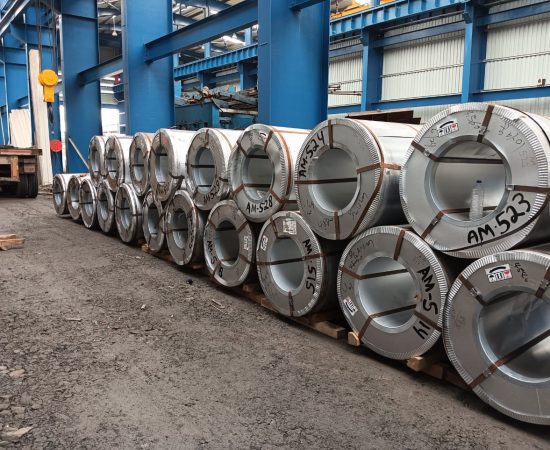
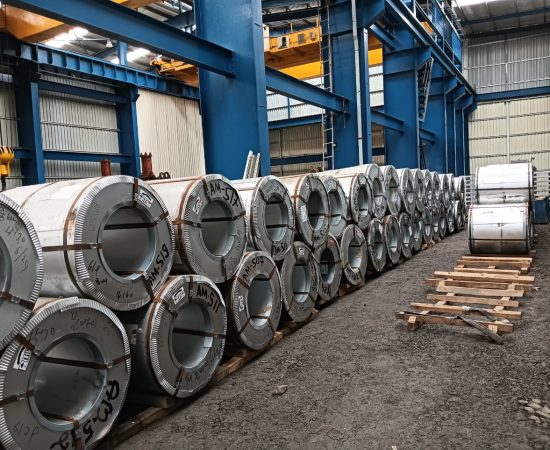
Aluminized steel is obtained by aluminizing, which is a modern day engineering innovation allowing manufacture of high-heat resistance aluminized steel sheets, coils and plates at low costs with niche applications.
Aluminizing, above all, is a thermo-chemical diffusion process & is particularly applied to base metals like carbon steel, alloy steel, stainless steel, nickel-based alloys & nickel-iron alloys.
Physical properties of the aluminized product so obtained depends on the base metal used as well as the coating process & coating agents namely aluminium or its alloys. Demonstrably, the aluminized products, all the more, show good resistance to oxidation as well as excellent corrosion resistance by contrast to Galvanized steel products.
There are 2 types of Aluminized Steel: Type 1 & Type 2.
Interchange of Type 1 with Type 2 or vice versa is not possible as each has specific properties as mentioned below.
Type 1 : Stainless Steel (309 or 439) or mild steel are hot-dip coated with aluminium/silicon alloy in such a way that a thin layer of aluminium/silicon alloy is obtained. The product is heat & corrosion resistant.
The aluminized coated mild steel (ACMS) is heat resistant to 4500C, whereas, on the other hand, the aluminized coated stainless steel (ACSS) is heat resistant upto 8500C.
Type 2 : Aluminized steel is hot-dipped in commercially pure aluminium. The products is used where corrosion resistance is required.
For most part, the Aluminized Steel has:
Better performance
Longer-life
Better cost efficacy
Higher thermal conductivity compared to stainless steel
Low thermal coefficient of expansion & thus does not changes shape like stainless steel
Electrostatic surface, thus allows it to be used in making exhaust systems & mufflers
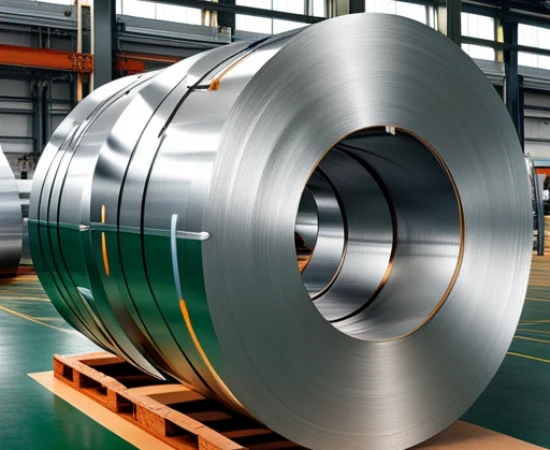
Aluminized Coated Steel sheets are manufactured ordinarily using coating bath of aluminium-silicon alloy which usually has 5 to 11% silicon & balance pure aluminium. The silicon additionally promotes better adherence. The manufacturing is done by continuous hot dipping of the base metal & consequently both sides are coated at the same time. The process assures a tight metallurgical bond between the base metal sheet as well as the aluminium-silicon coating. Subsequently these sheets have unique properties which are neither of base metal nor aluminium alone.
The base metals used are either Mild Steel (MS) or Stainless Steel (SS).
ALIOTA-M is Aluminized Coated Mild Steel
ALIOTA-S is Aluminized Coated Stainless Steel (Type 409 or 439)
Moreover, the ALIOTA-M is especially used for heat-resisting applications as well as where corrosion resistance & heat are involved.
(ASTM A463/A 463M-06)
All the below mentioned base metals will be designated as ALIOTA-M
Mild Steel {Commercial Steel (CS Types A, B, C)}
Forming Steel (FS) or Drawable Steel
Deep Drawing Steel (DDS)
Extra Deep drawing Steel (EDSS)
Structural Steel (SS) {these have many grades & classes}
High Strength-Low Alloy Steel (HSLAS Type A) {these have many grades & classes}
High Strength-Low Alloy Steel (HSLAS Type B) {these have many grades & classes}
All the below mentioned base metals will be designated as ALIOTA-S
Ferritic Stainless Steel (FSS Type 409) & Ferritic Stainless Steel (FSS Type 439)
ALIOTA-M Product Features
Product | Advantages | Uses |
ALIOTA-M | Beautiful surfaces formed due to suppressed crystal formation of melted aluminium during solidification | Home appliances Automobile parts Steel cans Oil pipeline cover (post-plated products) |
Even surface & excellent corrosion resistance created due to sacrificial effect of aluminium | ||
Excellent heat & corrosion resistance including paintability |
Comparative uses of ALIOTA-M & ALIOTA-S
ALIOTA-M | Home appliances Automobile parts Steel cans Oil pipeline cover (post-plated products) |
ALIOTA-S | Building material for interior & exterior Fuel cells Solar cell modules Automobile exhaust systems |
Heat Resistance of ALIOTA-M
ALIOTA-M has excellent heat resistance when compared with Zn-coated steel sheet, 55% Al-Zn alloy coated steel & cold rolled steel sheet.
ALIOTA-M shows no change in appearance or discoloration even if heated to long times ate temperatures of 4000C. However, above 4000C, the surface transforms to a layer of Al-Fe alloy which creates discoloration, however, the heat & corrosion resistant properties remain intact upto about 6000C.
Transformation of coated layer on heating is depicted below:
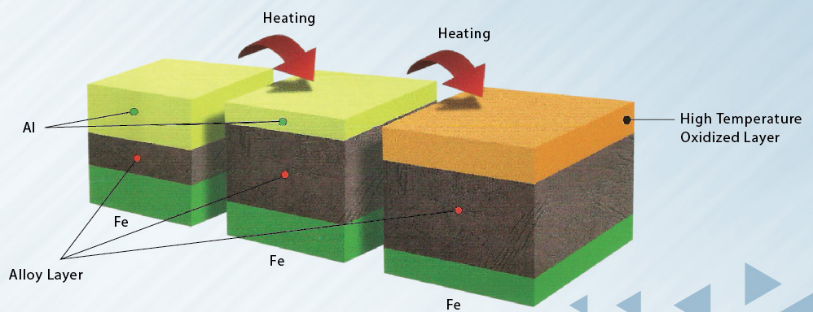
Discoloration & Heat Reflectivity
ALIOTA-M has beautiful surface & excellent heat reflectivity, therefore used in manufacture of toasters, gas ranges, oil stoves, gas ovens, clothes dryer etc.
A comparison of ALIOTA-M with Galvanized Steel (GL), Galvanized Iron (GI) & ZM sheet metals is shown below for Discoloration & Heat Reflectivity using parameters: 4000C; 24 hours.
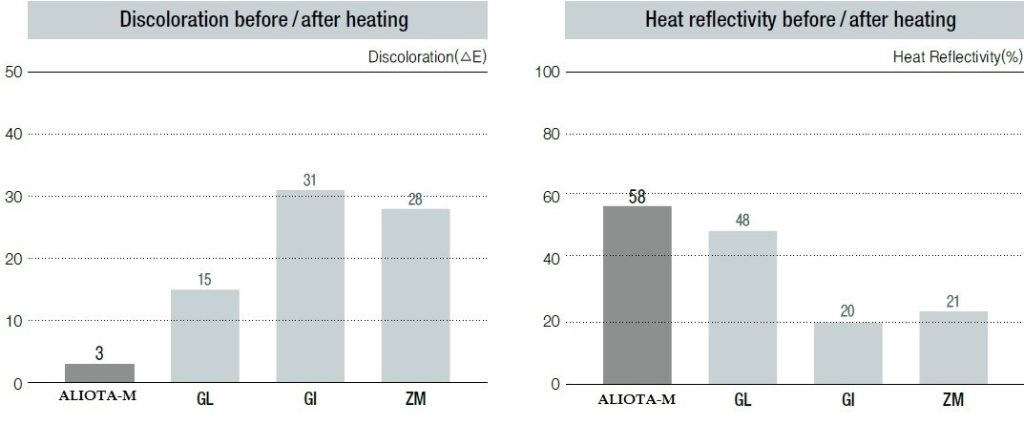
Corrosion Resistance of ALIOTA-M
ALIOTA-M can form a thin layer of oxides & hydroxides in presence of air & water. This makes it resistant to corrosion. In fact, even in acidic solutions it shows excellent corrosion resistance as compared to galvanized steel sheets. Amount of corrosion is in g/m2/day.
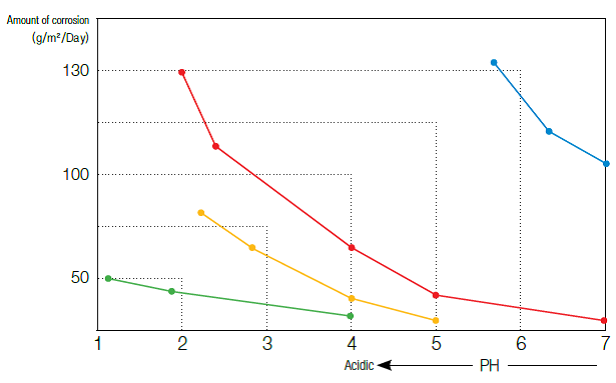
Salt Water Spray Test
ALIOTA-M shows excellent corrosion resistance & is proved by the Salt Water Spray Test data. Al shows higher electrode resistance as compared to Fe. As Fe is cathodized, Al prevents corrosion of Fe, acting as a sacrificial anode.
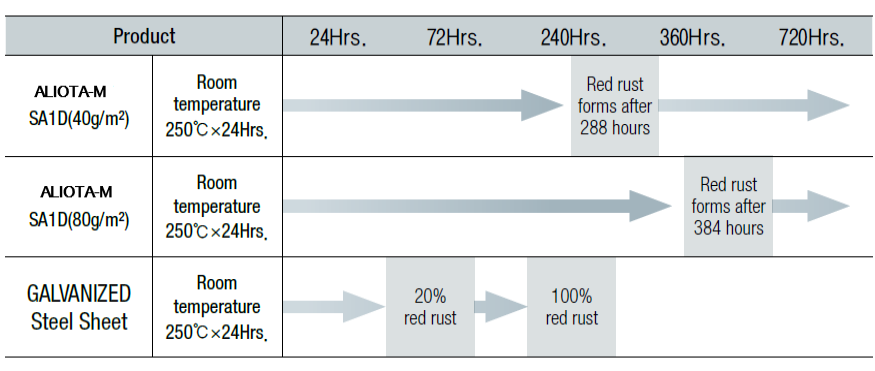
Corrosion Resistance Test In Exhaust Gases
ALIOTA-M & stainless steel show similar resistance against corroding effect of exhaust gases. Comparison of corrosion rate is shown below using cold-rolled steel sheet at base of 100% (87µm)
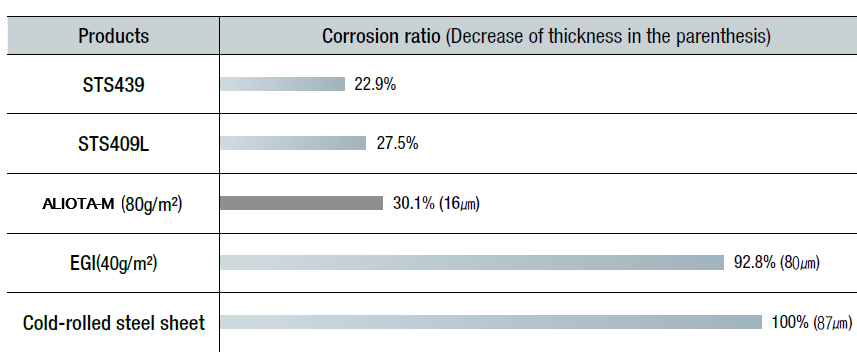
Weatherability
ALIOTA-M offers excellent resistance in severely corrosive environments like light & heavy industrial areas as well as urban areas. Outdoor exposure effects on ALIOTA-M as compared to Galvanized steel sheet are as below. ALIOTA-M shows no change in weatherability even if it turns brown in external environment.
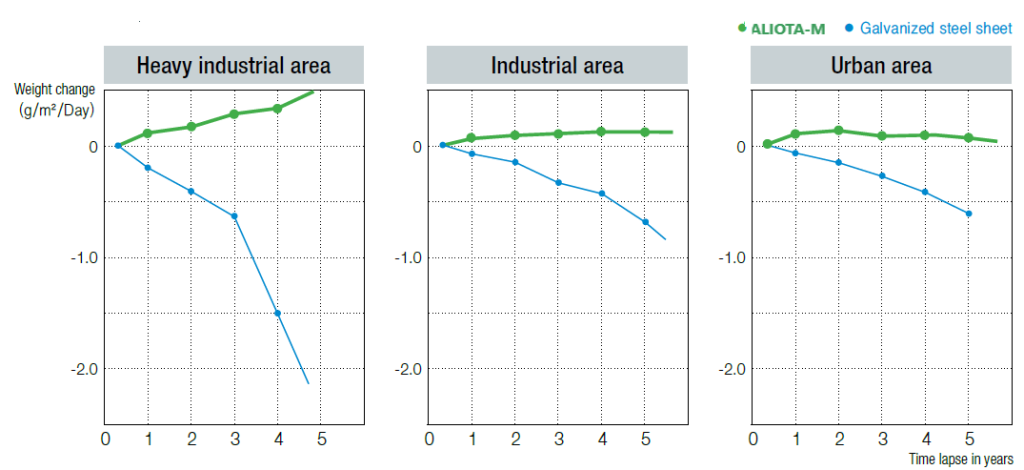
Corrosion Resistance Test In Exhaust Gases
ALIOTA-M has better processability as compared to cold-rolled sheets. The mechanical properties of ALIOTA-M are as follows:
Product | Type | Symbol (KS/JIS) | Tensile Tests | ||
ALIOTA-M | Yield Strength (MPa) | Tensile Strength (MPa) | Elongation (%) | ||
Commercial Quality | SA1C | ≥ 226 | ≥ 294 | – | |
Drawing Quality | SA1D | ≥ 206 | ≥ 284 | ≥ 36 | |
Deep Drawing Quality | SA1E | ≥ 196 | ≥ 275 | ≥ 40 |
(specimen thickness: 0/8 mm ; figures are for general values of 0.8T)
Paintability
ALIOTA-M can be painted better than galvanized steel sheet by chemical pre-treatment as shown below.
Paints based on the following types can be used: Vinyl Resins, silicone resins, phenolic resin, polyurethane resin & lacquers.
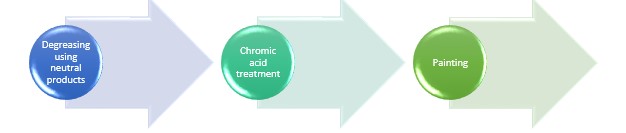
Standard comparison
Classification | KS D 3544 | JIS G 3314 | ASTM A 463 | DIN EN 10346 |
Commercial Quality | SA1C | SA1C | CS | DX51D |
Drawing Quality | SA1D | SA1D | - | DX52D, 53D |
Deep Drawing Quality | SA1E | SA1E | DDS | DX54D |
Extra Deep Drawing Quality | - | - | EDDS | DX56D |
Minimum coating weight (double side)
Coating weight symbol | Minimum coating weight for 3 points on both sides | Minimum coating weight for 1 point on both sides | KS D 3544 | JIS G 3314 | ASTM A 463 | DIN EN 10346 |
40 | 40 | 30 | 40 | 40 | T1-13(40) | – |
60 | 60 | 45 | 60 | 60 | – | AS 060 |
80 | 80 | 60 | 80 | 80 | T1-25(75) | – |
100 | 100 | 75 | 100 | 100 | – | AS 100 |
120 | 120 | 90 | – | 120 | T1-40(120) | – |
160 | 160 | 120 | – | – | – | – |
Width (W) Thickness(t) | W<1000 | Mark |
0.40≤ t <0.60 | ± 0.07 | ± 0.07 |
0.60≤ t <1.00 | ± 0.10 | ± 0.10 |
1.00≤ t <1.60 | ± 0.13 | ± 0.14 |
1.60≤ t <2.30 | ± 0.17 | ± 0.18 |
2.30≤ t | ± 0.21 | ± 0.22 |
KS, JIS
Width (W) Thickness(t) | W≤1500 |
t≤0.4 | ±0.08 |
0.4±0.10 |
|
1.0±0.13 |
|
1.5±0.15 |
|
2.0±0.30 |
|
ASTM
Thickness tolerance
Thickness(t) | W≤1200 | 1200 |
T ≤ 0.40 | ±0.05 | ±0.06 |
0.40±0.05 | ±0.06 |
|
0.60±0.06 | ±0.07 |
|
0.80±0.07 | ±0.08 |
|
1.00±0.08 | ±0.09 |
|
1.20±0.11 | ±0.13 |
|
1.60±0.14 | ±0.15 |
|
2.00±0.16 | ±0.17 |
|
DIN EN
Minimum coating weight (double side)
Coating weight symbol | Minimum coating weight for 3 points on both sides | Minimum coating weight for 1 point on both sides | KS D 3544 | JIS G 3314 | ASTM A 463 | DIN EN 10346 |
40 | 40 | 30 | 40 | 40 | T1-13(40) | – |
60 | 60 | 45 | 60 | 60 | – | AS 060 |
80 | 80 | 60 | 80 | 80 | T1-25(75) | – |
100 | 100 | 75 | 100 | 100 | – | AS 100 |
120 | 120 | 90 | – | 120 | T1-40(120) | – |
160 | 160 | 120 | – | – | – | – |
Ks D 3544
Classification | Symbol | Elongation(%) | Bending | |||
0.4≤t<0.6 | 0.6≤t<1.0 | 1.0≤t | Bend Angle | Inner Spacing od Bend | ||
Commercial Quality | SA1C | - | - | - | 180˚ | 4t |
Drawing Quality | SA1D | ≧30 | ≧32 | ≧34 | 180˚ | 1t |
Deep Drawing Quality | SA1E | ≧34 | ≧36 | ≧38 | 180˚ | 1t |
JIS G 3314
Classification | Symbol | Tensile strength (MPa) | Yield strength (MPa) | Elongation(%) | Bending | ||||
0.3≤ t <0.4 | 0.4t<0.6 | 0.6< t≤1.0 | 1.0≤ t | Bend Angle | Inner Spacing od Bend | ||||
Commercial Quality | SA1C | (≥205) | (≥270) | - | - | - | - | 180˚ | 4t |
Drawing Quality | SA1D | - | ≥280 | (≥28) | ≥30 | ≥32 | ≥34 | 180˚ | 1t |
Deep Drawing Quality | SA1E | - | ≥270 | - | ≥34 | ≥36 | ≥38 | 180˚ | 1t |
DIN EN 10364
Classification | Symbol | Yield strength(MPa) | Tensile strength(MPa) | EL(%) |
Commercial Quality | DX51D | - | 270~500 | ≥22 |
Drawing Quality | DX52D | 140~300 | 270~420 | ≥26 |
DX53D | 140~260 | 270~380 | ≥30 | |
Deep Drawing Quality | DX54D | 120~220 | 260~350 | ≥34 |
Extra Deep DrawingQuality | DX56D | 120~180 | 260~350 | ≥39 |
ASTM A 463
Classification | Symbol | Yield strength(MPa) | EL(%) |
Commercial Quality | CS Type A | 170~345 | ≥20 |
CS Type B | 205~345 | ≥20 | |
CS Type C | 170~380 | ≥15 | |
Drawing Quality | DDS | 140~240 | ≥32 |
Deep Drawing Quality | EDDS | 125~205 | ≥38 |
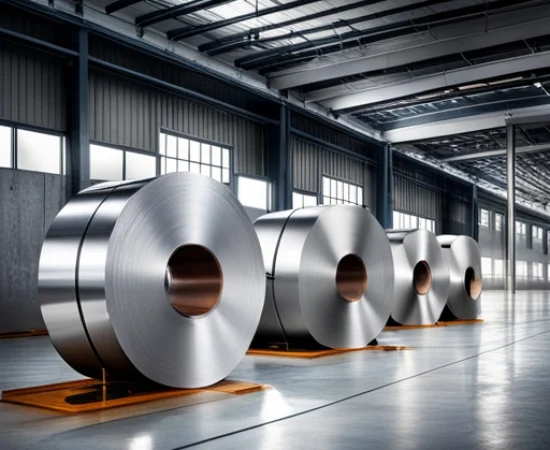
Aluminized Steel is steel coated on both sides with commercially pure Aluminium & is called as Aluminized Steel Type 2; ALIOTA-S. Thus, the attractive feature of the Type 2 aluminized steel is that they economically combine the surface characteristics of aluminium accompanied by the strength & rigidity of stainless steel.
Coating Type 2 is intended principally for use in applications requiring corrosion resistance & is available only as a coating on Commercial Steel, Forming Steel, Structural Steel as well as High Strength-Low Alloy Steel.
The process of making aluminized steel Type 2 is done by dipping appropriate steel in hot molted pure Aluminium (99.9%) & thus called hot dip coated Aluminized Steel.
The coating of aluminium comprises of two layers viz.
- an aluminium layer &
- an underlying hard aluminium-iron (Al-Fe) intermetallic alloy layer.
The total weight of Aluminium coating on Type 2 Aluminized Steel is about twice that on Type 1, or approximately 1.0 oz/ft2, (305.152 g/m2) which is equivalent to 0.002 in. (2 mils) thickness per side.
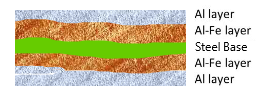
LAYERS OF ALUMINIZED STEEL TYPE 2
The Al-Fe layer is formed by the interaction of molten commercial pure aluminium with the steel surface (which has Fe) & this bonds the coating to the base metal firmly. The intermetallic alloy layer also supplements the aluminium layer & acts as a second line of defense to ensure long term durability in corrosive conditions. Control & uniformity in the alloy layer thickness assures the degree of coating necessary for manufacturing various products, for example corrugated steel pipes.
Uses
ALUMINIZED Steel Type 2, ALIOTA-S, has excellent atmospheric corrosion resistance as well as fire resistance. For this reason, it is principally intended to be used for these applications. For instance, Aluminized Steel Type 2, ALIOTA-S, is widely used in refineries, chemical as well as petrochemical industries.
Furthermore, ALIOTA-S, due to its excellent atmospheric corrosion resistance it is used as an excellent weather proofing material. This undoubtedly makes it the best option for insulations in coastal areas, offshore & on-shore oil & gas industrial installations for providing metallic jacketing.
ALIOTA-S offers good hot & cold insulation along with sound insulation.
It is widely used in Europe, Middle East as well as USA.
Aluminized Steel Type 2, ALIOTA-S, can be used for roofing & drainage systems, as well as insulation cladding (hot and cold), freshwater drainage, storm water detention systems, corrugated roofing & siding, drying ovens, air-conditioner condenser housings as well as grain bins for storing dry grains for human & animal consumption.
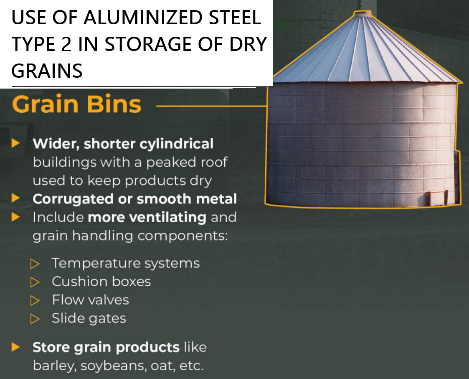
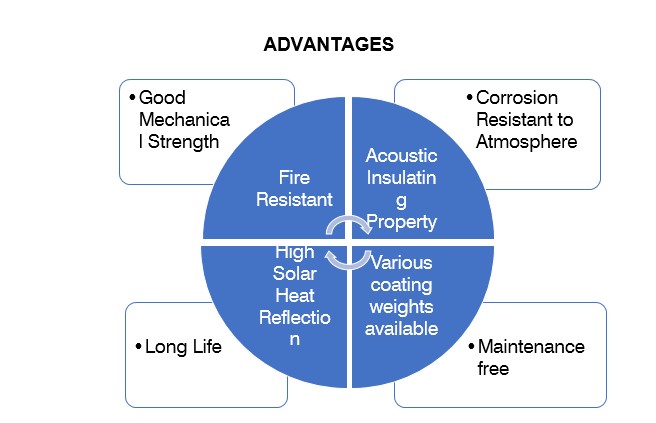
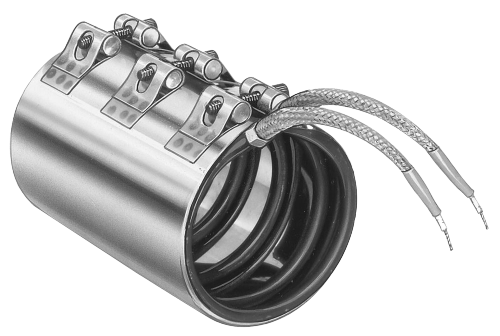
Band heater
Aluminized steel band heater is a type of steel that has been coated with an aluminum-silicon alloy to enhance its properties. Aluminized steel is widely used in the manufacturing of band heaters due to its excellent thermal and corrosion resistance properties. A band heater is a type of heating element that is wrapped around a cylinder or pipe to provide heat. The aluminized steel used in band heaters creates a highly efficient, durable, and cost-effective solution for heating applications. The aluminum coating on the steel provides excellent heat transfer properties, allowing the band heater to maintain a consistent temperature. Band heaters are commonly used in many industries, including plastics, oil and gas, food processing, and packaging. With the use of aluminized steel, band heaters become long-lasting and an effective solution for heating applications.
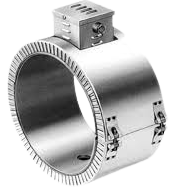
Mica heater
Aluminized steel mica heater is coated with aluminum and is commonly used in automotive exhaust systems, construction materials, and household appliances. Aluminized steel is also used to manufacture mica heaters, thin, flat heaters used for high-temperature applications. Mica heaters consist of a thin sheet of insulation with a heating element sandwiched between two layers of aluminized steel. This design provides excellent heat transfer and protection for the heating element, making mica heaters a popular choice in food processing, medical instruments, aerospace, and plastic industries. By combining aluminized steel with mica heaters, an efficient and reliable heating solution is provided for a wide range of applications.
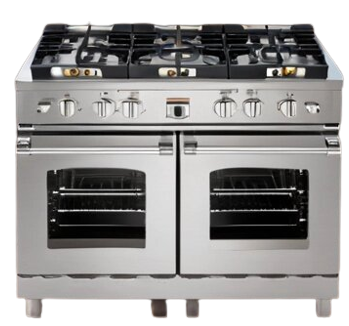
Gas range
Aluminized steel gas range is a type of cooking appliance that is commonly used in homes and commercial kitchens for preparing meals. It is made with a steel base or frame that is coated with a layer of aluminum to provide a rust-resistant and heat-resistant surface. The heat is typically controlled by knobs or dials on the front of the range, which allow the user to adjust the flame intensity. Aluminized steel gas ranges are popular because of their durability, affordability, and ability to withstand high temperatures.
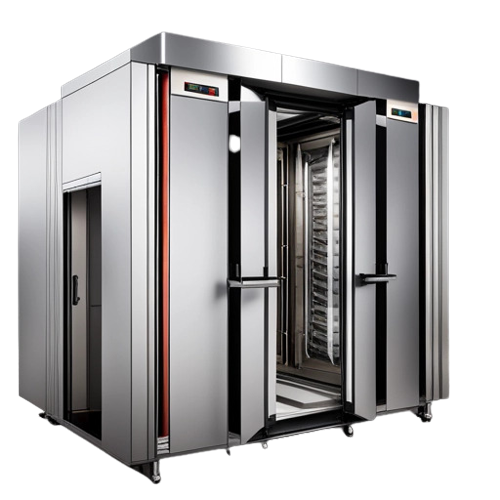
Microwave oven
Aluminized steel microwave oven is a type of microwave oven that is made of a combination of steel and aluminum. The steel provides durability and strength, while the aluminum coating helps to reflect the microwaves inside the cavity of the oven. This allows for even cooking and heating of food items, as the microwaves are evenly distributed throughout the cavity.
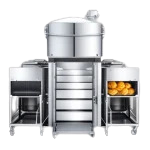
Dryer
Aluminized steel dryer is a type of clothes dryer that features a drum made of aluminized steel. The aluminized steel provides better protection against rust and wear than regular steel. The dryer is designed to spin wet clothes inside the drum while heated air is blown through them, evaporating the water and leaving the clothes dry. Aluminized steel dryers are very durable, and they can endure high temperatures without warping or cracking. Additionally, aluminized steel dryers are very quiet and produce less noise than other types of dryers. They are a popular choice for households that want a reliable and efficient way to dry clothes quickly and conveniently.
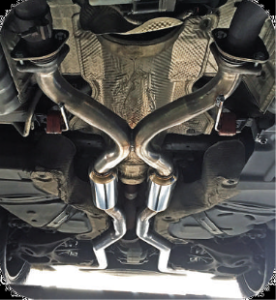
Exhaust
Aluminized steel exhaust system Improved car exhaust systems are now required to meet Bharat Stage VI emissions standards. Aluminized steel Type 1 is an ideal material for coating exhaust systems as it can withstand high temperatures and thereby control emissions, supporting compliance with global emission regulations.
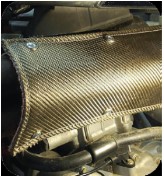
Heat shield
Aluminized steel heat shields sensitive automobile parts from engine and exhaust-generated heat. With 80% reflectivity, it acts as a cost-effective heat shield that remains shiny up to 4000C. Shields are placed under car parts and around the engine to prevent overheating.
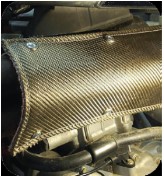
Heat shield
Aluminized steel heat shields sensitive automobile parts from engine and exhaust-generated heat. With 80% reflectivity, it acts as a cost-effective heat shield that remains shiny up to 4000C. Shields are placed under car parts and around the engine to prevent overheating.
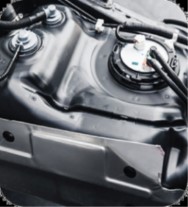
Fuel tanks
Aluminized steel Fuel tanks made of cold rolled and mild steel can corrode due to impurities in petrol, diesel, and bio-diesel. This leads to rust particles floating in the fuel which adversely affects the engine and automobile performance. The use of aluminized steel is recommended as it is strong and resistant to corrosion by almost all petroleum and synthetic fluids.
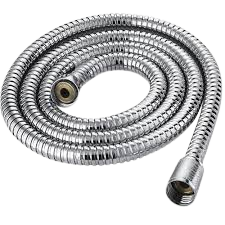
Hose Pipe
Aluminized steel hose pipes are flexible tubing made with a steel core coated or laminated with aluminum, resistant to heat and corrosion. They’re used in chemical processing, vehicles’ exhaust systems, and industrial manufacturing. Hot-dipping or thermal spraying applies the aluminum. These lightweight pipes are durable, withstand high pressure and temperatures, and have high thermal conductivity. They’re preferred over other pipes due to their resistance to rust, oxidation, and other forms of corrosion, making them ideal for applications where heat transfer is essential. Aluminized steel hose pipes offer a reliable and cost-effective solution and meet the demands for durability, flexibility, resistance to corrosion and heat.
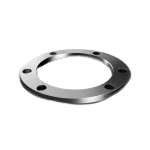
Gasket
Aluminized steel gasket is a type of sealing material used to create a tight seal between two surfaces in machinery, engines, and other industrial applications. This type of gasket typically consists of a steel core surrounded by a layer of aluminum on both sides. The aluminum layer provides excellent resistance to corrosion, while the steel core provides strength and durability. The gasket functions by compressing between the two surfaces to fill any imperfections and provide a seal that prevents leaks and loss of pressure. Aluminized steel gaskets are commonly used in high-temperature and high-pressure environments, such as in exhaust systems, engines, and industrial boilers. They are also useful in applications where resistance to corrosion and oxidation is essential.
Heat resistance
Aluminized steel for the most part shows neither change in appearance nor discoloration even if heated for long times at temperatures of 4000C. However, above 4000C, the surface transforms to a layer of Al-Fe alloy which usually creates discoloration, however, heat as well as corrosion-resistant properties remain intact up to about 6000C.
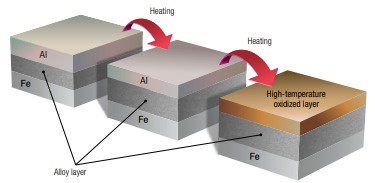
Corrosion resistance
Aluminized steel also forms a thin layer of oxides & hydroxides in the presence of air as well as water. Finally, this makes it resistant to corrosion. In fact, even in acidic solutions, it shows excellent corrosion resistance as compared to galvanized steel sheets. Besides, the amount of corrosion is in g/m2/day.
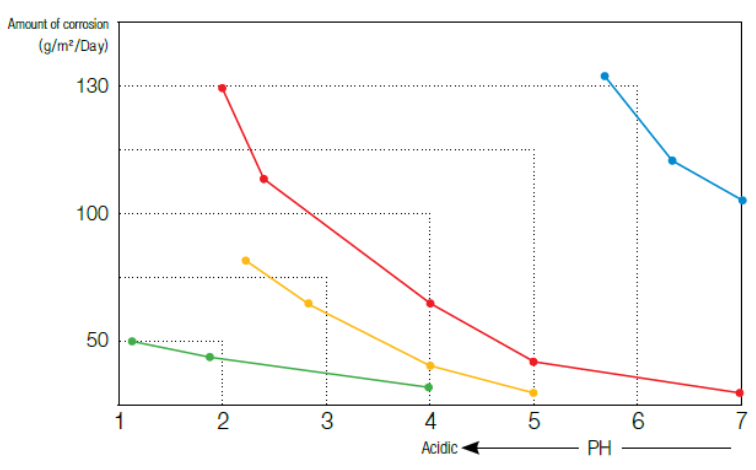
Salt water spray test
Aluminized steel salt water spray test shows excellent corrosion resistance & is proved by the Salt Water Spray Test data. Al shows higher electrode resistance as compared to Fe. As Fe is cathodized, Al prevents corrosion of Fe & acting as a sacrificial anode.
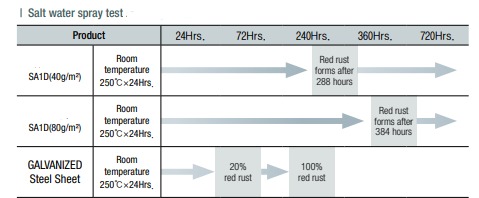
Heat Reflectivity
Aluminized steel has a beautiful surface as well as excellent heat reflectivity, therefore used in manufacture of toasters, gas ranges, oil stoves, gas ovens as well as clothes dryer etc.
Comparison of with Galvanized Steel (GL), Galvanized Iron (GI) & ZM sheet metals is shown below for Discoloration as well as Heat Reflectivity using parameters: 4000C; 24 hours.
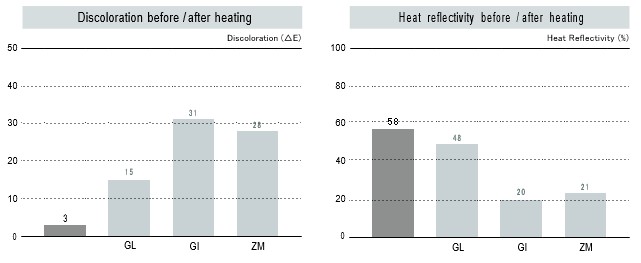
Processability
Aluminized steel has better Processability as compared to cold-rolled sheets. The mechanical properties are as follows:
Product | Type | Symbol (KS/JIS) | Tensile test | ||
Yield strength (MPa) | Tensile strength (MPa) | Elongation (%) | |||
AS | Commercial Quality | SA1C | ≥ 226 | ≥ 294 | – |
Drawing Quality | SA1D | ≥ 206 | ≥ 284 | ≥ 36 | |
Deep Drawing Quality | SA1E | ≥ 196 | ≥ 275 | ≥ 40 |
Paintability
Aluminized steel Can be painted better than galvanized steel sheets by chemical pre-treatment as shown below.
Paints based on the following types can be used: Vinyl Resins, silicone resins, phenolic resin, polyurethane resin & lacquers.
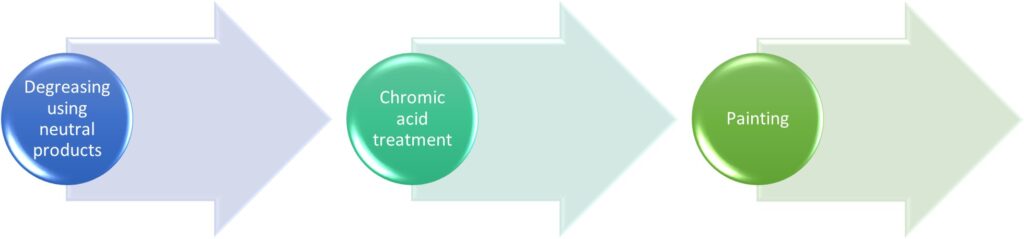
Weatherability
Aluminized steel has excellent resistance in severely corrosive environments like light & heavy industrial areas as well as urban areas. The sheet shows no change in weatherability even if it turns brown in the external environment.
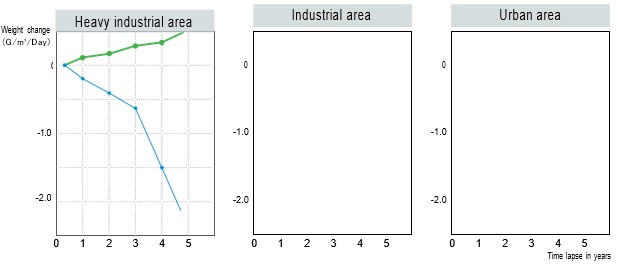
Standard comparison
Classification | KS D 3544 | JIS G 3314 | ASTM A 463 | DIN EN 10346 |
Commercial Quality | SA1C | SA1C | CS | DX51D |
Drawing Quality | SA1D | SA1D | - | DX52D, 53D |
Deep Drawing Quality | SA1E | SA1E | DDS | DX54D |
Extra Deep Drawing Quality | - | - | EDDS | DX56D |
Minimum coating weight (double side)
Coating weight symbol | Minimum coating weight for 3 points on both sides | Minimum coating weight for 1 point on both sides | KS D 3544 | JIS G 3314 | ASTM A 463 | DIN EN 10346 |
40 | 40 | 30 | 40 | 40 | T1-13(40) | – |
60 | 60 | 45 | 60 | 60 | – | AS 060 |
80 | 80 | 60 | 80 | 80 | T1-25(75) | – |
100 | 100 | 75 | 100 | 100 | – | AS 100 |
120 | 120 | 90 | – | 120 | T1-40(120) | – |
160 | 160 | 120 | – | – | – | – |
Width (W) Thickness(t) | W<1000 | Mark |
0.40≤ t <0.60 | ± 0.07 | ± 0.07 |
0.60≤ t <1.00 | ± 0.10 | ± 0.10 |
1.00≤ t <1.60 | ± 0.13 | ± 0.14 |
1.60≤ t <2.30 | ± 0.17 | ± 0.18 |
2.30≤ t | ± 0.21 | ± 0.22 |
KS, JIS
Width (W) Thickness(t) | W≤1500 |
t≤0.4 | ±0.08 |
0.4±0.10 |
|
1.0±0.13 |
|
1.5±0.15 |
|
2.0±0.30 |
|
ASTM
Thickness tolerance
Thickness(t) | W≤1200 | 1200 |
T ≤ 0.40 | ±0.05 | ±0.06 |
0.40±0.05 | ±0.06 |
|
0.60±0.06 | ±0.07 |
|
0.80±0.07 | ±0.08 |
|
1.00±0.08 | ±0.09 |
|
1.20±0.11 | ±0.13 |
|
1.60±0.14 | ±0.15 |
|
2.00±0.16 | ±0.17 |
|
DIN EN
Minimum coating weight (double side)
Coating weight symbol | Minimum coating weight for 3 points on both sides | Minimum coating weight for 1 point on both sides | KS D 3544 | JIS G 3314 | ASTM A 463 | DIN EN 10346 |
40 | 40 | 30 | 40 | 40 | T1-13(40) | – |
60 | 60 | 45 | 60 | 60 | – | AS 060 |
80 | 80 | 60 | 80 | 80 | T1-25(75) | – |
100 | 100 | 75 | 100 | 100 | – | AS 100 |
120 | 120 | 90 | – | 120 | T1-40(120) | – |
160 | 160 | 120 | – | – | – | – |
Ks D 3544
Classification | Symbol | Elongation(%) | Bending | |||
0.4≤t<0.6 | 0.6≤t<1.0 | 1.0≤t | Bend Angle | Inner Spacing od Bend | ||
Commercial Quality | SA1C | - | - | - | 180˚ | 4t |
Drawing Quality | SA1D | ≧30 | ≧32 | ≧34 | 180˚ | 1t |
Deep Drawing Quality | SA1E | ≧34 | ≧36 | ≧38 | 180˚ | 1t |
JIS G 3314
Classification | Symbol | Tensile strength (MPa) | Yield strength (MPa) | Elongation(%) | Bending | ||||
0.3≤ t <0.4 | 0.4t<0.6 | 0.6< t≤1.0 | 1.0≤ t | Bend Angle | Inner Spacing od Bend | ||||
Commercial Quality | SA1C | (≥205) | (≥270) | - | - | - | - | 180˚ | 4t |
Drawing Quality | SA1D | - | ≥280 | (≥28) | ≥30 | ≥32 | ≥34 | 180˚ | 1t |
Deep Drawing Quality | SA1E | - | ≥270 | - | ≥34 | ≥36 | ≥38 | 180˚ | 1t |
DIN EN 10364
Classification | Symbol | Yield strength(MPa) | Tensile strength(MPa) | EL(%) |
Commercial Quality | DX51D | - | 270~500 | ≥22 |
Drawing Quality | DX52D | 140~300 | 270~420 | ≥26 |
DX53D | 140~260 | 270~380 | ≥30 | |
Deep Drawing Quality | DX54D | 120~220 | 260~350 | ≥34 |
Extra Deep DrawingQuality | DX56D | 120~180 | 260~350 | ≥39 |
ASTM A 463
Classification | Symbol | Yield strength(MPa) | EL(%) |
Commercial Quality | CS Type A | 170~345 | ≥20 |
CS Type B | 205~345 | ≥20 | |
CS Type C | 170~380 | ≥15 | |
Drawing Quality | DDS | 140~240 | ≥32 |
Deep Drawing Quality | EDDS | 125~205 | ≥38 |
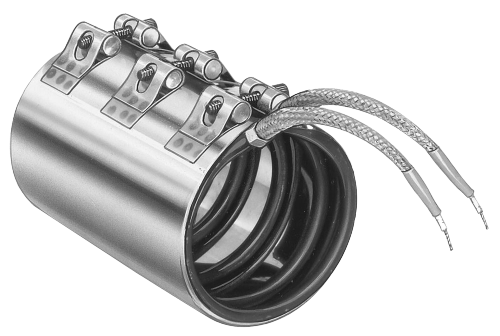
Band heater
Aluminized steel band heater is a type of steel that has been coated with an aluminum-silicon alloy to enhance its properties. Aluminized steel is widely used in the manufacturing of band heaters due to its excellent thermal and corrosion resistance properties. A band heater is a type of heating element that is wrapped around a cylinder or pipe to provide heat. The aluminized steel used in band heaters creates a highly efficient, durable, and cost-effective solution for heating applications. The aluminum coating on the steel provides excellent heat transfer properties, allowing the band heater to maintain a consistent temperature. Band heaters are commonly used in many industries, including plastics, oil and gas, food processing, and packaging. With the use of aluminized steel, band heaters become long-lasting and an effective solution for heating applications.
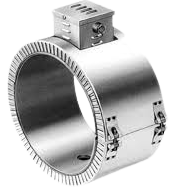
Mica heater
Aluminized steel mica heater is coated with aluminum and is commonly used in automotive exhaust systems, construction materials, and household appliances. Aluminized steel is also used to manufacture mica heaters, thin, flat heaters used for high-temperature applications. Mica heaters consist of a thin sheet of insulation with a heating element sandwiched between two layers of aluminized steel. This design provides excellent heat transfer and protection for the heating element, making mica heaters a popular choice in food processing, medical instruments, aerospace, and plastic industries. By combining aluminized steel with mica heaters, an efficient and reliable heating solution is provided for a wide range of applications.
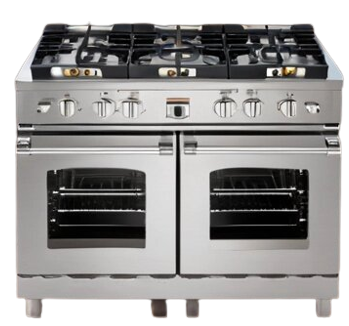
Gas range
Aluminized steel gas range is a type of cooking appliance that is commonly used in homes and commercial kitchens for preparing meals. It is made with a steel base or frame that is coated with a layer of aluminum to provide a rust-resistant and heat-resistant surface. The heat is typically controlled by knobs or dials on the front of the range, which allow the user to adjust the flame intensity. Aluminized steel gas ranges are popular because of their durability, affordability, and ability to withstand high temperatures.
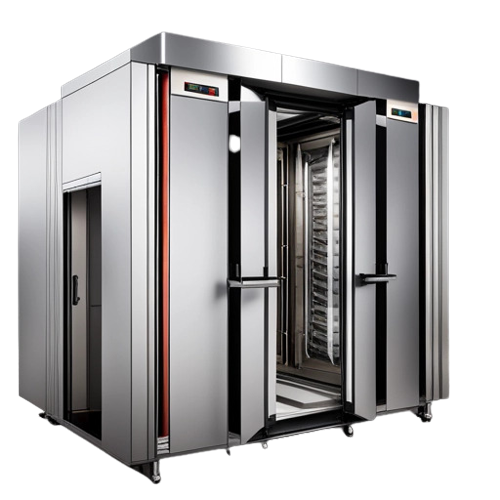
Microwave oven
Aluminized steel microwave oven is a type of microwave oven that is made of a combination of steel and aluminum. The steel provides durability and strength, while the aluminum coating helps to reflect the microwaves inside the cavity of the oven. This allows for even cooking and heating of food items, as the microwaves are evenly distributed throughout the cavity.
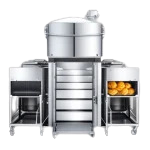
Dryer
Aluminized steel dryer is a type of clothes dryer that features a drum made of aluminized steel. The aluminized steel provides better protection against rust and wear than regular steel. The dryer is designed to spin wet clothes inside the drum while heated air is blown through them, evaporating the water and leaving the clothes dry. Aluminized steel dryers are very durable, and they can endure high temperatures without warping or cracking. Additionally, aluminized steel dryers are very quiet and produce less noise than other types of dryers. They are a popular choice for households that want a reliable and efficient way to dry clothes quickly and conveniently.
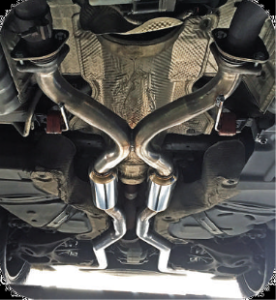
Exhaust
Aluminized steel exhaust system Improved car exhaust systems are now required to meet Bharat Stage VI emissions standards. Aluminized steel Type 1 is an ideal material for coating exhaust systems as it can withstand high temperatures and thereby control emissions, supporting compliance with global emission regulations.
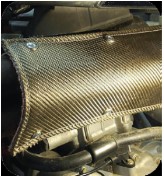
Heat shield
Aluminized steel heat shields sensitive automobile parts from engine and exhaust-generated heat. With 80% reflectivity, it acts as a cost-effective heat shield that remains shiny up to 4000C. Shields are placed under car parts and around the engine to prevent overheating.
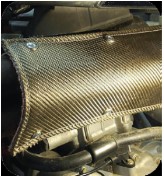
Heat shield
Aluminized steel heat shields sensitive automobile parts from engine and exhaust-generated heat. With 80% reflectivity, it acts as a cost-effective heat shield that remains shiny up to 4000C. Shields are placed under car parts and around the engine to prevent overheating.
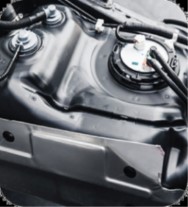
Fuel tanks
Aluminized steel Fuel tanks made of cold rolled and mild steel can corrode due to impurities in petrol, diesel, and bio-diesel. This leads to rust particles floating in the fuel which adversely affects the engine and automobile performance. The use of aluminized steel is recommended as it is strong and resistant to corrosion by almost all petroleum and synthetic fluids.
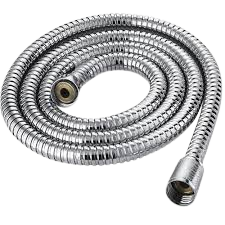
Hose Pipe
Aluminized steel hose pipes are flexible tubing made with a steel core coated or laminated with aluminum, resistant to heat and corrosion. They’re used in chemical processing, vehicles’ exhaust systems, and industrial manufacturing. Hot-dipping or thermal spraying applies the aluminum. These lightweight pipes are durable, withstand high pressure and temperatures, and have high thermal conductivity. They’re preferred over other pipes due to their resistance to rust, oxidation, and other forms of corrosion, making them ideal for applications where heat transfer is essential. Aluminized steel hose pipes offer a reliable and cost-effective solution and meet the demands for durability, flexibility, resistance to corrosion and heat.
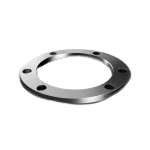
Gasket
Aluminized steel gasket is a type of sealing material used to create a tight seal between two surfaces in machinery, engines, and other industrial applications. This type of gasket typically consists of a steel core surrounded by a layer of aluminum on both sides. The aluminum layer provides excellent resistance to corrosion, while the steel core provides strength and durability. The gasket functions by compressing between the two surfaces to fill any imperfections and provide a seal that prevents leaks and loss of pressure. Aluminized steel gaskets are commonly used in high-temperature and high-pressure environments, such as in exhaust systems, engines, and industrial boilers. They are also useful in applications where resistance to corrosion and oxidation is essential.
Related Products
- International
- Domestic
- Asia
- North America
- South America
- Europe
- Africa
- Australia
Asia
North America
Europe
Africa
Australia
-
East India
- West India
- North India
- South India
- Union Territories of India
Balod, Baloda Bazar, Balrampur, Bastar, Bemetara, Bijapur, Dantewada, Dhamtari, Durg, Gariaband, Janjgir Champa, Jashpur, Kabirdham, Kanker, Kondagaon, Korba, Koriya, Mahasamund, Mungeli, Narayanpur, Raigarh, Raipur, Rajnandgaon, Sukma, Surajpur, Surguja, Moudhapara, Birgoan, Lalpur, Nahar Para, Devpuri, Bilaspur, Rajnandgaon, Dagori , Tilda, Lara, Silphari , Siltara, Champa, Jamul.
Angul, Boudh (Baudh), Balangir, Bargarh, Balasore (Baleswar), Bhadrak, Cuttack, Deogarh (Debagarh), Dhenkanal, Ganjam, Gajapati, Jharsuguda, Jajpur, Jagatsinghapur, Khordha, Keonjhar (Kendujhar), Kalahandi, Kandhamal, Koraput, Kendrapara, Malkangiri, Mayurbhanj, Nabarangpur, Nuapada, Nayagarh, Puri, Rayagada, Sambalpur, Subarnapur (Sonepur), Sundargarh, Kataka, Rayagada,.
Alipurduar, Bankura, Birbhum, Cooch Behar, Dakshin Dinajpur, Darjeeling, Hooghly, Howrah, Jalpaiguri, Jhargram, Kalimpong, Kolkata, Malda, Murshidabad, Nadia, North 24 Parganas, Paschim Bardhaman, Paschim Medinipur, Purba Bardhaman, Purba Medinipur, Purulia, South 24 Parganas, Uttar Dinajpur, Tangra, Haldia, Bilkanda, Bajitpur, Rameshwerpur, Barrackpore, Dasnagar, Bagh, Dankunibil, Nandal, Sahalalpur, Domjur, Rajhat, Tegharia, Narendra Chandra Dutta Sarani, Chandni Chawk, B.B.D. Bagh,Bowbazar, Maheshtala, Asansol, Belghoria, Tikiapara,
East Sikkim, North Sikkim, South Sikkim, West Sikkim, Gangtok, Mangan, Namchi, Geyzing.
Bokaro, Chatra, Deoghar, Dhanbad, Dumka, East Singhbhum, Garhwa, Giridih, Godda, Gumla, Hazaribagh, Jamtara, Khunti, Koderma, Latehar, Lohardaga, Pakur, Palamu, Ramgarh, Ranchi, Sahebganj, Seraikela, Simdega,West Singhbhum, Aditpapur, Gamharia, Ahirtoli, Tatisilwai, Gamharia, Hazaribagh, haranganj, Kumhartoli, Pandra, Bokaro Steel City, Argora, Delatoli, Medininagar, Dhanbad, Hatia, Jumala, Tensera, Tudupana, Kokar, Namkum, Tatisilwai, Chapawar, Koilari, Sarwal, Kulhi, Burmu, Patratu, Barhi, Sikri, Daltonghanj, Koderma, Belchampa, Lohardagga, Barghi, Babhani, Sikri, Belchampa.
Baksa, Barpeta, Biswanath, Bongaigaon, Cachar, Charaideo, Chirang, Darrang, Dhemaji, Dhubri, Dibrugarh, Dima Hasao, Goalpara, Golaghat, Hailakandi, Hojai, Jorhat, Kamrup Metropolitan, Kamrup, Karbi Anglong, Karimganj, Kokrajhar, Lakhimpur, Majuli, Morigaon, Nagaon, Nalbari, Sivasagar, Sonitpur, South Salmara-Mankachar, Tinsukia, Udalguri, West Karbi Anglong, Silchar, North Guwahati, Bijni, Margherita, Barpeta Road, Sonari, Kharupetia, Dhekiajuli, Jagiroad, Guwahati, Lanka, Tezpur, Lumding, Amguri, Ambikapur, Chabua, Lakhipur, Gohpur, Jogighopa, Badarpur, Duliajan, Moran, Diphu, Hamren, Abhayapuri, Marigaon, Rangapara, New Bongaigaon Railway Colony, Bokajan, Mangaldai, Haflong, Numaligarh, Silchar Part-X, Doboka, Digboi Oil Town, Sibsagar, Biswanath Chariali, Dergaon, Bokokhat, Bilasipara, Silapathar, Dispur.
Changlang, East Kameng, East Siang, Lohit, Lower Subansiri, Papum-Pare, Tawang, Tirap, Upper Siang, Upper Subansiri, West Siang, Anjaw, Lower Dibang Vally, Kurung Kumey, Namsai, Ziro, West Kameng, Naharlagun, Papum Pare, Pasighat, Tezu, Basar, Itanagar, Roing, Khonsa, Doimukh, Namsai, Chimpu, Pasighat, Itanagar, Namsai.
Dhalai, North Tripura, West Tripura, South Tripura, Ambassa, Kailasahar, Udaipur, Agartala, Khowai, Indranagar, Kanchanpur, Kailasahar.
Araria, Arwal, Aurangabad, Banka, Begusarai, Bhagalpur, Bhojpur, Buxar, Darbhanga, East Champaran, Gaya, Gopalganj, Jamui, Jehanabad, Khagaria, Kishanganj, Kaimur, Katihar, Lakhisarai, Madhubani, Munger, Madhepura, Muzaffarpur, Nalanda, Nawada, Patna, Purnia, Rohtas, Saharsa, Samastipur, Sheohar, Sheikhpura, Saran, Sitamarhi, Supaul, Siwan, Vaishali, West Champaran, Bettiah, Hajipur, Dumra, Arrah, Motihari, Bhabua, Bihar Sharif, Sasaram, Chhapra, Dumra,Sitamarhi, Piro, Jogbani, Bihariganj, Raxaul, Daudnagar, Hisua, Chakia, Nirmali, Motipur, Ramnagar, Asarganj, Ghoghardiha, Bikramganj, Dinapur Cantonment, Nokha, Dehri, Kanti, Jagdispur, Teghra, Jhanjharpur, Habibpur, Mairwa, Areraj, Dalsingh Sarai, Amarpur, Jamalpur, Dhaka, Barh, Masaurhi, Mohiuddinagar, Naugachhia, Maharajganj, Chhatapur, Forbesganj, Bihar, Rajgir, Marhaura, Chanpatia, Barhiya, Narkatiaganj, Lalganj, Jaynagar, Islampur, Phulwari, Ara, Bodh Gaya, Mokama, Colgong, Ghrounda, Deedarganj , Chhoti Pahari, Chapra, Hajipur, Mohanbariam, Madhopara, Gehumi, Kaghzi Mohalla.
East Garo Hills, East Khasi Hills, Jaintia Hills,Ri Bhoi,South Garo Hills,West Khasi Hills, Williamnagar, Shillong, Jowai, Nongpoh , Baghmara, Tura, Nongstoin, West Garo Hills, Shillong Cantonment, Jawai, Nongthymmai.
Thoubal, Imphal East, Imphal West, Senapati, Ukhrul, Chandel, Churachandpur, Tamenglong, Nambol, Imphal, Jiribam, Bishnupur, Moreh, Kakching.
Aizawl, Kolasib, Lawngtlai, Lunglei, Mamit, Saiha, Serchhip, Champhai.
Dimapur, Kiphire, Kohima, Longleng, Mokokchung, Mon, Peren, Phek, Tuensang, Wokha, Zunheboto, Noklak.
Ahmednagar, Akola, Amravati, Aurangabad,v Beed, Bhandara, Buldhana, Chandrapur, Dhule, Gadchiroli, Gondia, Hingoli, Jalgaon, Jalna, Kolhapur, Latur, Mumbai, Nagpur, Nanded, Nandurbar, Nashik, Osmanabad, Palghar, Parbhani, Pune, Raigad, Ratnagiri, Sangli, Satara, Sindhudurg, Solapur, Thane, Wardha, Washim, Yavatmal, Kalamboli, Taloja, Vasai, Vashi, Mira Bhayandar, Bhiwandi, Ulhasnagar, Ambarnath, Panvel, Degaon , Kupwad, Waluj , Avadhan , Tarapur, Boisar, Pimpri, Chinchwad , Satpur, Ambad, Sinnar, Butibori, Kagal , Gokul Shirgaon, Shiroli, Akola, Mahad, Rabale, Turbhe, Kalyan, Chandrapur, Lote, Beed. Osnambad, Satna, Nagothane.
Ahmedabad, Amreli, Anand, Aravalli, Banaskantha, Bharuch, Bhavnagar, Botad, Chhota Udaipur, Dahod, Dang, Devbhoomi Dwarka, Gandhinagar, Gir Somnath, Jamnagar, Junagadh, Kutch, Kheda, Mahisagar, Mehsana, Morbi, Narmada, Navsari, Panchmahal, Patan, Porbandar, Rajkot, Sabarkantha, Surat, Surendranagar, Tapi, Vadodara, Valsad, Palanpur, Veraval, Bhuj, Lunavada, Rajpipla, Godhra, Himmatnagar, Vyara, Dahej, Sanand ,Vani, Vatwa, Dhandhuka, Dholka, Viramgam, Kathawada, Odhav, Naroda, Sankheda, Sankheda, Dabhoi, Ranoli, Limbda, Por Ramangamdi, Nandesari, Makarpura, Vaghodia, Savli, Thasra, Kapadwanj, Matar, Nadiad, Balasinor, Sojitra, Umreth, Petlad, Borsad, Khambat, V.U. Nagar, Bhat,Dehgam, Mansa, Ranasan, Gozaria, Pardi, Bhilad, Umbergaon, Sarigam , Vapi, Unai, Bilimora, Dhrol, Bhatia, Bhanvad, Jamkhambhalia, Arambhada, Kotda-Sangani, Paddhari, Malia, Jasdan, Bhaktinagar, Jetpur, Wankaner, Morbi, Dhoraji, Gondal, Rafaleshwar, Kuvadawa, Aji, Lodhika, Valod, Khatodara, Bardoli, Nizarm, Olpad, Katargam, Doswada, Pandesaram, Hazira, Sachin, Ichchapore, Jafrabad, Liliya, Rajula, Babra, Damnagar, Amrelim, Babra, Vallabhipur, Dhasa, Botad, Vitthalwadi, Shihor, Palitana, Mahuva, Shihor, Vertej, Alang, Chitra, Sihori, Ambaji, Radhanpur, Chandisar, Mundra, Madhapur, Anjar, Mandvi, Vagra, Jambusar, Hansot, Panoli, Nabipur, Dungari, Valia, Naldhari, Kanerao, Dodwada, Kondh, Atali-Kaladra, Ankleshwar, Jhagadia, Tilakwada, Sagbara, Dediapada, Rajpipla, Visavadar, Veraval, Sutrapada, Porbandar, Miyani, Sayla, Chotila, Lakhtar, Halvad, Thangadh, Dhangadhra, Limbdi, Bamanbore, Kukarwada, Balisana, Kheralu, Visnagar, Vijapur, Kalol, Kadi, Chhatral, Patan, Chanasma, Lanva, Sidhpur, Jambughoda, Shahera, Godhra, Halol, Devgadhbaria, Malpur, Idar, Modasa, Himatnagar, Talod, Pimpri, Rakhial, Odhav, Sarkhej, Dhanera, Alang, Dharangadhra, Deea, Gandhidham, Karjan, Vartej, Kapadwanj, Pardi, Kanjari, Kaliawadi, Mithapur, Bhachau, Patan, Tapi, Sayla, Amroli.
North Goa, South Goa, Mapusa, Bicholim, Panaji, Bardez, Tiswadi, Bicholim, Sattari, Pernem, Mormugao, Ponda, Quepem, Margao and Dharbandora. Salcete, Sanguem, Canacona, Bethora, Bicholim, Canacona, Colvale, Corlim, Cuncolim, Dharbandoda, Honda, Kakoda, Kundaim, Latambarcem, Madkaim, Mapusa, Margao Panchwadi, Pilerne, Pissurlem, Quittol, Sancoale, Sanguem, Shiroda, Thivim, Tuem,Verna, Pilerna, Porvorim,
Bilaspur, Chamba, Hamirpur, Kangra, Kinnaur,Kullu,Lahaul & Spiti, Mandi, Shimla , Sirmaur, Solan, Una, Baddi, Sheetalpur , Sundar Nagar, Sirmour, Pataliyon, Una, Indora, Bari, Damtal, Mehatpur, Gagret, Parwano, Barotiwala, Shamshi, Nagrotu Bagwan,Sansar Pur Tera, Solan, Mandi, Hamirpur, Shogi, Raga-Ka-Bagh, Ambi, Taliwala, Keylong.
Amritsar, Barnala, Faridkot, Fatehgarh Sahib, Firozpur, Fazilka, Gurdaspur, Hoshiarpur, Ludhiana,, Moga, Sri Muktsar Sahib, Pathankot, Patiala, Rupnagar, Sahibzada Ajit Singh Nagar, Sangrur, Shahid Bhagat Singh Nagar, Taran Taran, Dhilwan, Dasuya, Dinanagar, Karoran, Samrala, Malaut, Kurali, Mandi Gobindgarh, Jaitu, Nabha, Payal, Balachaur, Muktsar, Moonak, Khamanon, Batala, Bassi Pathana, Guru Har Sahai, Bhadur, Sahnewal, Lalru, Sanaur, Longowal, Jagraon, Sardulgarh, Phillaur, Anandpur Sahib, Mohali, Nawanshahr, Banga, Dera Bassi, Bhikhi, Malerkotla, Doraha, Garhshankar, Kharar, Sirhind, Shahkot, Zirakpur, Khanna, Rampura, Ludhiana, Mansa, Dhuri, Makhu, Amloh, Urmar Tanda, Raman, Goraya, Jalandhar Cantonment, Hoshiarpur, Kartarpur, Bhuch, Malout, Rajpura, Kotkapura, Sunam, Giddarbaha, Dirba, Firozpur Cantonment, Dhariwal, Morinda, Naya Nangal, Hariana, Nakodar, Phagwara, Machhiwara, Ajnala, Sultanpur Lodhi, Tarn Taran, Maur, Zira, Alawalpur, Ghagga, Kot Kapura, Kapurthala, Pattran, Jalalabad, Bagh Purana, Bathinda, Nawashahr, Budhlada, Munak, Bhabat, Bhawanigarh, Abohar, Hajipur, Ahmedgarh, Sujanpur, Samana, Jalandhar, Sahib, Gurdaspur, Nangal,, Mukerian, Talwandi Bhai, Lehra Gaga.
Pithoragarh,Uttarkashi, Rishikesh Cantonment, Rishikesh, Dehradun, Bhim Tal, Mahua Kheraganj, Khatima, Kausani, Bageshwar, Kashipur, Sitarganj, Srinagar, Dehrakhas, Tehri, Haridwar, Narendranagar, Nainital, Vikasnagar, Kotdwara, Ramnagar, Masuri, Rurki, Roorkee, Udham Singh Nagar, Laksar, Kaladungi, Sultanpur, Almora, Manglaur, Kichha, Chamoli and Gopeshwar, Gadarpur, Chakrata, Champawat, Lalkuan, Rudraprayag, Rudrapur, Jaspur, Haldwani, Ranipur, Ranikhet, Pauri, Bazpur, Tanakpur, Chamoli, Pauri Garhwal.
Bhiwani, Charkhi Dadri, Faridabad, Fatehabad, Gurugram, Hisar, Jhajjar, Jind, Kaithal, Karnal, Kurukshetra, Mahendragarh, Nuh, Palwal, Panchkula, Panipat, Rewari, Rohtak, Sirsa, Sonipat, Yamunanagar, Ladwa, Indri, Punahana, Siwani, Asandh, Raipur Rani, Ateli, Barwala, Kheri Sampla, Hodal, Ratiya, Kalka, Narayangarh, Uklana Mandi, Bahadurgarh, Tauru, Gohana, Rania, Pundri, Dharuhera, Ballabgarh, Pehowa, Gurgaon, Ghraunda, Tohana, Kanina, Narwana, Narnaund, Gannaur, Shahabad, Pinjaur, Dabwali, Chita, Samalkha, Hansi, Safidon, Taraori, Kharkhoda, Bawal, Thanesar, Kalanwali, Ellenabad, Loharu, Jagadhri, Radaur, Nilokheri, Maham, Kundli, Bilaspur, Sohna, Ambala Cantt, Narnaul, Farrukhnagar, Firozpur Jhirka, Julana, Beri,Ambala
Ringas, Sirohi, Jhalawar, Bhasawar, Khairthal, Didwana, Bari Sadri, Napasar, Chittorgarh, Kherwara Chhaoni, Kota, Ratangarh, Bharatpur, Barmer, Chhabra, Raisinghnagar, Pushkar, Mangrol, Kumbhalgarh, Bilara, Kuchaman, Chhoti Sadri, Sambhar, Suratgarh, Churu, Asind, Nawalgarh, Kankroli, Raipur, Rajgarh, Aklera, Devgarh, Dausa, Khetri, Pilani, Jaisalmer, Pali, Beawar, Ramgarh, Sangariya, Udpura, Pipar, Nimaj, Vijainagar, Abu Road, Bagru, Bundi, Shahpura, Indragarh, Sumerpur,Balotra, Baswa, Sunel, Gothra, Mount Abu, Surajgarh, Sujangarh, Pratapgarh, Ratan Nagar, Karauli, Dholpur, Chirawa, Bali, Marwar, Gangapur, Ladnun, Hindaun, Swaroopganj, Nathdwara, Deoli, Jhunjhunun, Rajsamand, Kapasan, Kishangarh, Rani, Nasirabad, Bhadra, Neemrana, Bandikui, Jaiselmer, Bikaner, Rawatbhata, Amet, Salumbar, Jhalrapatan, Falna, Rawatsar, Taranagar, Sagwara, Neem Ka Thana, Lakheri, Begun, Padampur, Dungarpur, Udaipur, Chomun, Basi, Phalodi, Pokaran, Bahror, Sardarshahr, Sikar, Jodhpur, Anupgarh, Lachhmangarh, Makrana, Chhipa Barod, Bhinmal, Kekri, Bari, Bhilwara, Jaitaran, Sriganganagar, Nawa, Kuchera, Alwar, Pilibanga, Mandawar, Kaman, Niwai, Pindwara, Jalore, Merta, Newa Talai, Sheoganj, Sojat Road, Hanumangarh, Sawai Madhopur, Ramganj Mandi, Fatehnagar, Kot Putli, Nokha, Nagar, Baran, Nohar, Bhawani Mandi, Ajmer, Nimbahera, Sojat, Malpura, Lalsot, Jaipur, Rajakhera, Bijoliya Kalan, Nagaur, Madanganj, Bhawri, Ganganagar, Raniwara, Mundwa, Sadulshahar, Sadri, Tijara, Phulera, Fatehpur, Banswara, Bhiwadi, Bayana, Sanchor, Tonk.
Aligarh, PrayagRaj, Ambedkar Nagar, Amroha, Auraiya, Azamgarh, Badaun, Bahraich, Ballia, Balrampur, Banda District, Barabanki, Bareilly, Basti, Bijnor, Bulandshahr, Chandauli(Varanasi Dehat), Chitrakoot, Deoria, Etah, Etawah, Faizabad, Farrukhabad, Fatehpur, Firozabad, Gautam Buddha Nagar, Ghaziabad, Ghazipur, Gonda, Gorakhpur, Hamirpur, Hapur District, Hardoi, Hathras, Jaunpur District, Jhansi, Kannauj, Kanpur Dehat, Kanpur Nagar, Kasganj, Kaushambi, Kushinagar, Lakhimpur Kheri, Lalitpur, Lucknow, Maharajganj, Mahoba, Mainpuri, Mathura, Mau, Meerut, Mirzapur, Moradabad, Muzaffarnagar, Pilibhit, Pratapgarh, Rae Bareli, Rampur, Saharanpur, Sant Kabir Nagar, Sant Ravidas Nagar, Sambhal, Shahjahanpur, Shamli, Shravasti, Siddharthnagar, Sitapur, Sonbhadra, Sultanpur, Unnao, Varanasi (Kashi), Allahabad, Amethi, Bagpat, Baheri, Bilsi, Bilaspur, Maghar, Chandausi, Mubarakpur, Palia Kalan, Sadabad, Sahanpur, Jalaun, Lakhimpur, Kurara, Anpara, Gopiganj, Chhata, Sandila, Harraiya, Jewar, Robertsganj, Ramkola, Khekra, Bharthana, Kiratpur, Fatehabad, Sikandra Rao, Jyotiba Phule Nagar, Nautanwa, Jhansi Cantonment, Chilkana Sultanpur, Bangarmau, Usawan, Jais, Tilhar, Fatehpur Chaurasi, Deoband, Khatauli, Rudarpur, Beswan, Kanpur, Tundla, Nawabganj, Kerakat, Jalalabad, Aliganj, Dibiyapur, Purdil Nagar, Sirsaganj, Orai, Biswan, Dhanaura, Shikarpur, Behat, Hasanpur, Sikandarabad, Gautam Buddh Nagar, Modinagar, Nihtaur, Chitrakut Dham, Nichlaul, Khamaria, Bikapur, Jalesar, Loni, Barhani, Musafirkhana, Jasrana, Jansath, Varanasi, Jalalpur, Vrindavan, Kota, Sikandra, Gajraula, Khalilabad, Beniganj, Sardhana, Babrala, Bahjoi, Kundarki, Puranpur, Siyana, Baraut, Phaphund, Agra, Rampura, Ramnagar, Muradnagar, Dhampur, Pilkhuwa, Najibabad, Bilsanda, Dudhinagar, Gola Gokarannath, Greater Noida, Mathura Cantonment, Bindki, Kosi Kalan, Ganj Muradabad, Nagina, Bhatpar Rani, Alapur, Prayagraj Cantonment, Mankapur, Manikpur, Sahaswan, Bilari, Chandpur, Varanasi Cantonment, Bisalpur, Faizabad Cantonment, Bidhuna, Aurangabad, Fatehgarh, Kalpi, Lalganj, Renukut, Bisauli, Dibai, Karhal, Bilhaur, Sherkot, Nakur, Rasra, Seohara, Safipur, Hapur, Daurala, Kishni, Anupshahr, Obra, Rath, Dasna, Tanda, Gunnaur, Barva Sagar, Konch, Mauranipur, Jaunpur, Kishanpur, Bareilly Cantonment, Thakurdwara, Shahganj, Kunda, Ayodhya, Bulandshahar, Mawana, Miranpur, Kanth, Kharkhoda, Budaun, Gursahaiganj, Bhinga, Colonelganj, Zamania, Pandit Deendayal Upadhyay Nagar, Chandauli, Sirsa, Bhadohi, Sidhpura, Rae Bareilly, Karnawal, Sarsawan, Noida, Gyanpur, Shikohabad, Bhongaon, Shahjahanpur Cantonment, Gangoh, Gokul, Khurja, Hata, Sahibabad, Patti, Gulaothi, Anandnagar, Fatehpur Sikri, Chunar, Ghosia Bazar, Mursan, Pahasu, Nizamabad, Agra Cantonment, Kheri, Hyderabad, Kairana, Banda, Dadri.
Balod, Baloda Bazar, Balrampur, Bastar, Bemetara, Bijapur, Bilaspur, Dantewada, Dhamtari, Durg, Gariaband, Janjgir-Champa, Jashpur, Kabirdham, Kanker, Kondagaon, Korba, Koriya, Mahasamund, Mungeli, Narayanpur, Raigarh, Raipur, Rajnandgaon, Sukma, Surajpur, Surguja, Pathalgaon, Dongragarh, Bilha, Kharsia, Saraipali, Mahendragarh, Tildanewra, Jashpurnagar, Champa, Khairagarh, Sarajpur, Bhatapara, Bagbahara, Kurud, Bhilai, Pendra, Baloda, Jagdalpur, Katghora, Sarangarh, Kawardha, Pithora, Ramanuj Ganj, Kumhari, Telgaon, Chirmiri, Bemetra, Kota, Ambikapur, Dongargaon, Sakti, Urla, Charoda.
Agar Malwa, Alirajpur, Anuppur, Ashoknagar, Balaghat, Barwan, Betul, Bhind, Bhopal, Burhanpur, Chhatarpur, Chhindwara, Damoh, Datia, Dewas, Dhar, Dindori, East Nimar, Guna, Gwalior, Harda, Hoshangabad, Indore, Jabalpur, Jhabua, Katni, Mandla, Mandsaur, Morena, Narsinghpur, Neemuch, Niwari, Panna, Raisen, Rajgarh, Ratlam, Rewa, Sagar, Satna, Sehore, Seoni, Shahdol, Shajapur, Sheopur, Shivpuri, Sidhi, Singrauli, Tikamgarh, Ujjain, Umaria, Vidisha, West Nimar, Agar, Khandwa, Khargone, Sukhlia, Loha Mandi, Pithampur, Palda, Narmadapuram, Lasudia , Budasa, Patan, Shahpur, Sonkatch, Pachmarhi, Birsinghpur, Depalpur, Bagli, Parasia, Maksi, Mau, Sarangpur, Malaj Khand, Garoth, Begamganj, Khetia, Machalpur, Barwani, Biaora, Joura, Shahpura, Maihar, Kailaras, Jawad, Multai, Mangawan, Anjad, Sagar Cantonment, Beohari, Jaora, Panagar, Gohad, Karera, Pipliya Mandi, Amarpatan, Gormi, Sihora, Barwaha, Jirapur, Khujner, Manasa, Pichhore, Rajpur, Rampura, Maheshwar, Manawar, Katangi, Bagh, Kotma, Babai, Nalkheda, Alot, Khirkiya, Sanchi, Sitamau, Gairatganj, Malhargarh, Shamgarh, Dabra, Ichhawar, Gadarwara, Vijayraghavgarh, Basoda, Bamaniya, Nagod, Dhamnod, Shujalpur, Rau, Nepa Nagar, Kukshi, Rahatgarh, Betul Bazar, Banda, Pipariya, Udaipura, Badnagar, Bina-Etawa, Mhow, Khajuraho, Amarwara, Berasia, Sendhwa, Mandleshwar, Khurai, Sultanpur, Khilchipur, Jabalpur G.C.F, Baraily, Sausar, Tarana, Malanpur, Jabalpur Cantonment, Badnawar, Petlawad, Bijuri, Timarni, Sironj, Sohagpur, Mandideep, Kareli, Tekanpur, Harsud, Bhainsdehi, Pandhurna, Ashta, Hanumana, Ratlam Kasba, Khategaon, Itarsi, Kasrawad, Ganjbasoda, Chanderi, Rampur Baghelan, Bina Railway Colony, Kurwai, Sanawad, Chichli, Kothi, Nagda, Baihar, Indergarh,,
Perundurai, Thirumazhisai, Melur, Cuddalore, Theni Allinagaram, Kallakkurichi, Sayapuram, Agaram, Sivakasi, Thiruvithankodu, Maraimalai Nagar, Madhavaram, Vadalur, Musiri, Pudukkottai , Kundrathur, Srivaikuntam, Surandai, Bargur, Sholinganallur, Kodambakkam, Palladam, Mulanur, Punjaipugalur, Kelambakkam, Minambakkam, Pennagaram, Kotagiri, Jalakandapuram, Hosur, Bhavani, Tiruchchendur, Punjai Thottakurichi, Vadakarai Kizhpadugai, Ettaiyapuram, Ganapathipuram, Panruti, Ramapuram, Arcot, Vaniyambadi, Mudukulathur, Dhalavoipuram, Gingi, Kadayal, Ayyampettai, Natrampalli, Anaimalai, Kallidaikurichchi, Vadamadurai, Karaikkudi, Pernambut, Kamayagoundanpatti, Vijayapuri, Palayamkottai, Minjur, Thanjavur, Attur, Neyveli, Gandhi Nagar, Dharmapuri, Maduranthakam, Ulundurpettai, Auroville, Vaithiswarankoil, Paramakkudi, Kolachal, Kangayam, Kamuthi, Usilampatti, Vadakku Valliyur, Aralvaimozhi, Belur, Kadathur, Kariamangalam, Inam Karur, Odaiyakulam, Nagapattinam, Udankudi, Arimalam, Mallapuram, Pattiviranpatti, Tirupur, Kaliyakkavilai, Iluppur, Coonoor, Kariapatti, Uttamapalaiyam, Dharapuram, Annur, Vasudevanallur, Ariyalur, Kulithalai, Avadi, Manapparai, Ambasamudram, Tharangambadi, Athanur, Rameswaram, Taramangalam, Sankarankoil, Udagamandalam, Natham, Theni, Kumbakonam, Vellakoil, Kumarapuram, Mayiladuthurai, Alwar Tirunagari, Thiruvalam, Zamin Uthukuli, Coimbatore, Nasiyanur, Chennai, Namakkal, Pallipalaiyam, Vandavasi, Kelamangalam, Kottur, Madurai, Tiruvottiyur, Idappadi, Kalavai, Tiruvallur, Thirunirmalai, Mahabalipuram, Alangulam, Gudiyattam, Vikravandi, Perambalur, Singaperumalkoil, Kovilpatti, Vengavasal, Vilapakkam, Anthiyur, Karumathampatti, Thiruporur, Swamimalai, Madukkarai, Arantangi, Manavalakurichi, Pammal, Urapakkam, Valangaiman, Nagercoil, Singampuneri, Madippakkam, Kinathukadavu, Tirumangalam, Mangadu, Tirupattur, Harur, Puliyankudi, Pollachi, Thuthipattu, Perungalathur, Dindigul, Omalur, Komarapalayam, Thiruvarur, Parangippettai, Kambam, Pallipattu, Acharapakkam, Peraiyur, Sirumugai, Rasipuram, Srirangam, Virudhachalam, Adyar, Thisayanvilai, Polur, Vandalur, Nanguneri, Sattur, Tiruchengode, Aruppukkottai, Kuzhithurai, Kunnathur, Tindivanam, Devakottai, Alangudi, Uthangarai, Kottakuppam, Ranipet, Sankari, Sathyamangalam, Nallur, Sholingur, Tiruverambur, Sirkali, Ramanathapuram, Kolathur, Nannilam, Athani, Karur, Chennimalai, Kattuputhur, Salem, Sivagiri, Nilgiris, Kaveripattinam, Gobichettipalayam, Periyakulam, Cheyyar, Ambur, Chinalapatti, Papanasam, Tiruvannamalai, Aravakurichi, Mallur, Chinna Salem, Sivaganga, Erode, Udumalaipettai, Anakaputhur, Palakkodu, Arni, Maduravoyal, Virudhunagar, Kattumannarkoil, Pudukkottai, Tirupathur, Lalgudi, Tenkasi, Thondamuthur, Chennasamudram, Tirukkoyilur, Arakonam, Sulur, Melvisharam, Kollankoil, Chengalpattu, Ooty, Thiruthangal, Kalugumalai, Udayarpalayam, Krishnagiri, Gummidipoondi, Chembarambakkam, Peravurani, Tiruverkadu, Kayalpattinam, Punjai Puliyampatti, Tuticorin, Kalpakkam, Gangavalli, Srimushnam, Pattukkottai, Saravanampatti, Vilathikulam, Denkanikottai, Muthupet, Thirumalayampalayam, Guduvanchery, Chatrapatti, Madanur, Thuvakudi, Arani, Bhuvanagiri, Perungudi, Kanchipuram, Kodaikanal, Karamadai, Kanyakumari, Mukkudal, Huligal, Nellikkuppam, Panapakkam, Uthiramerur, Shenkottai, Kilvelur, Nilakkottai, Mettur, Kanakkampalayam, Mamallapuram, Gudalur, Thirunindravur, Puliyur, Tiruchirappalli, Uttukkuli, Villupuram, Mannargudi, Nerkunram, Tirunelveli, Manachanallur, Thottiyam, Walajapet, Ponneri, Kumarapalayam, Porur, Jayankondam, Mettupalayam, Valavanur, Vedaranniyam, Vriddhachalam, Srivilliputtur, Pappireddipatti, Orathanadu, Kadayanallur, Manamadurai, Puzhal, Palani, Edaikodu, Annavasal, Adiramapattinam, Oddanchatram, Avinashi, Mylapore, Valasaravakkam, Mattur, Pandamangalam, Chidambaram, Katpadi, Thevaram, Elayirampannai, Sriperumpudur, Madambakkam, Chinnammanur, Bodinayakkanur, Virakeralam, Thiruthuraipundi, Kilakarai, Rajapalayam, Vellore, Kallakurichi, Kanniyakumari, Thoothukudi, Tiruppur, Tiruvarur, Viluppuram, Ambattur, Parrys, Broadway, Guindy, Madhavaram, Padi, Sriperumbudur, Injambakkam, Mudichur, Park town, Sowcarpet, , Vadapalani, Teynampet, Velachery, Mannivakkam Perambur, Thuraipakkam, Tondiarpet.
Adilabad, Bhadradri Kothagudem, Hyderabad, Jagitial, Jangaon, Jayashankar Bhupalapally, Jogulamba Gadwal, Kamareddy, Karimnagar, Khammam, Kumarambheem Asifabad, Mahabubabad, Mahabubnagar, Mancherial district, Medak, Medchal–Malkajgiri, Mulugu, Nagarkurnool, Narayanpet, Nalgonda, Nirmal, Nizamabad, Peddapalli, Rajanna Sircilla, Ranga Reddy, Sangareddy, Siddipet, Suryapet, Vikarabad, Wanaparthy, Warangal Rural, Warangal Urban, Yadadri Bhuvanagiri, Adilabad, Kothagudem, Bhupalpalle, Gadwal, Asifabad, Mancherial, Shamirpet, Sircilla, Shamshabad, Warangal, Bhongir, Secunderabad, Ranigunj, Yellandu, Medchal, Manuguru, Palwancha, Patancheru, Ranga Reddy district, Miryalaguda, Sathupalle, Ramagundam, Bhainsa, Armoor, Narsampet, Ghatkesar, Jagtial, Zahirabad, Koratla, Tandur, Kodada, Gajwel, Bodhan, Sarapaka, Bhadrachalam.
Anantapur, Chittoor, East Godavari, Guntur, Kadapa, Krishna, Kurnool, Sri Potti Sri Ramulu Nellore, Prakasam, Srikakulam, Visakhapatnam, Vizianagaram, West Godavari, Kakinada, Machilipatnam, Nellore, Ongole, Eluru, Renigunta, Hukumpeta, Chirala, Rajam, Markapur, Kurmannapalem, Suriapet, Madanapalle, Mancheral, Razam, Kanigiri, Pendurthi, Palmaner, Mandapeta, West Godavari Dist., Alampur, Dharmavaram, Narsapur, Tadepalligudem, Pedana, Avanigadda, Ramachandrapuram, Tirvuru, Nandigama, Tadpatri, East Godavari Dist., Peddapuram, Qutubullapur, Gopalapatnam, Uppal Kalan, Bestavaripeta, Pamur, Sirsilla, Pedagantyada, Guti, Puttur, Rameswaram, Kamalapuram, Nagari, Chimakurthy, Kavali, Rajampet, Bapatla, Turangi, Anakapalle, Jammalamadugu, Proddatur, Srikalahasti, Dhone, Penugonda, Narasaraopet, Amur, Tirumala, Vetapalem, Tiruchanur, Palasa, Tuni, Guntakal, Amalapuram, Garacharma, Nandyal, Punganuru, Kuppam, Hindupur, Yemmiganur, Gudur, Sirpur, Rajendranagar, Choutuppal, Salur, Tekkali, Vemalwada, Narayanavanam, Bobbili, Sattenapalle, Mandasa, Gudivada, Adoni, Pulivendla, Chilakaluripet, Uravakonda, Kollapur, Prasantinilayam, Atmakur, Badvel, Trimulgherry, Tenali, Bhimavaram, Nuzvid, Chandur, Karnul, Cuddapah, Kazipet, Ravulapalam, Marturu, Betamcherla, Sulurpeta, Yadagirigutta, Pakala, Nidadavole, Godavarikhani, Repalle, Cumbum, Gannavaram, Nayudupeta, Narsipatnam, Tirupati, Rajahmundry, Palakole, Ajjaram, Samalkot, Kamareddi, Pithapuram, Vijayawada, Chinagantyada, Bapulapadu, Chodavaram, Tanuku, Macherla, Challapalle, Kadiri, Mahabubnagar, Yellamanchili, Akividu, Jaggayyapeta, Gajuvaka, Vinukonda, Kovvur, Singarayakonda, Seetharampuram, Kovur, Andole, Mangalagiri.
Bangalore / Bengaluru , Hubli, Belgaum , Mysuru / Mysore, Shivamogga, Gulbarga, Tumakuru, Davangere, Udupi, Ballari, Bidar, Dharwad , Hampi, Biljapur, Chitradurga, Badami, Hassan, Hosapete, Chikmaglur, Raichur, Gadag, Madikeri, Srirangapatna, Mandya, Bhadravathi, Bagalkot, Karwar, Belur, Uttara Kannada, Pattadakal, Gangavathi, Halebidu, Ranebennur, Hassan, Kolar, Dandeli, Gulbarga, Sringeri, Robertsonpet, Bijapur, Aihole, Manipal, Gadag, Devanahalli, Koppal, Kolar, Manipal, Doddaballapur, Sakleshpur, Karkala.
Kochi, Thiruvananthapuram, Tirvandrum, Kozhikode, Thrissur, Kollam, Kannur, Kottayam, Alappuzha, Palakkad, Munnar , Varkala , Thalassery, Kovalam, Kasaragod, Aluva, Perinthalmanna, Pathanamthitta, chalakuddy, Thodupuzha, Punalur, Tirur, Guruvayur, Kodungallur, Thiruvalla, Malappuram, Muvattupuzha, Kumarakom, Kollam, Tripunithura, Nilambur, Adoor, Kalpetta, Cherthala, Chegannur, Vadakara, Kayamkulam, Ottapalam, Kottarakkara, Vaikom, Ponnani, Kanhangad, Changanacherry, Mattancherry, Kothamangalam, Kalamassery, Koyilandy, Pala, Chavakkad, Perumbavoor, Beypore
Anantnag, Bandipore, Baramulla, Budgam, Doda, Ganderbal, Jammu, Kathua, Kishtwar, Kulgam, Kupwara, Poonch, Pulwama, Rajauri, Ramban, Reasi, Samba, Shopian district, Srinagar, Udhampur, Leh, Kargil, Kishtwar, Shupiyan, Ganderbal,Kartholi, Lassipora, Rangreth, Sopore, Shalteng, Lassipora, Ghatti, Budgam, Trikuta Nagar, Bakshi Nagar, Bishnah, Digiana, Kothi Bagh.
Central Delhi, North Delhi, South Delhi, East Delhi, North East Delhi, South West Delhi, New Delhi, North West Delhi, West Delhi, South Eest Delhi, Daryaganj, Sadar Bazaar, Saket, Preet Vihar, Shahdara, Palam, Connaught Place, Kanjhawala, Rajouri Garden, Defence Colony,Ajmeri Gate, Rohini, Nawada, Anand Parbat, Mundka.
South Andaman, North And Middle Andaman, Nicobars, Portblair, Mayabunder, Car Nicobar, Garacharma, Pahargaon,Pathergudda, Junglighat.
Kavaratti, Agethi
Daman, Diu, Dadra, Nagar Haveli, Naroli, Dabhel, Silvassa.
Karaikal, Mahe, Pondicherry, Yanam, Kurumbapet, Manavely, Ozhukarai, Thirumalairayanpattinam, Villianur, Puducherry.
Chandigarh